The majority of software programs have a set of minimum system requirements, including those for video cards, to ensure compatibility with a user’s computer hardware. Nevertheless, these requirements often only provide the bare minimum necessary to run the software and do not take into account the hardware that would offer optimal performance. In some instances, the lists can also be outdated, specify outdated hardware versions, or simply suggest inferior hardware options.
In an effort to provide a more reliable and accurate recommendation, we have conducted thorough testing to determine the hardware that performs best with SOLIDWORKS. As a result, we have created our own list of recommended hardware based on our findings.
CPU for SolidWorks
For SOLIDWORKS modelling, the ideal CPU choice is the Intel Core i7 13700K. This CPU is favoured due to its high operating frequency, which is crucial for fast performance in general modelling tasks in SOLIDWORKS such as opening and saving files, rebuilding assemblies, and rotating models. The Core i7 13700K boasts high clock speeds and improved per-core performance, as well as additional efficient cores for handling background tasks and multithreading, allowing the main cores to focus on active workloads. If even more power is desired, the Core i9 13900K offers higher clock speeds and additional efficiency cores for improved multi-tasking.
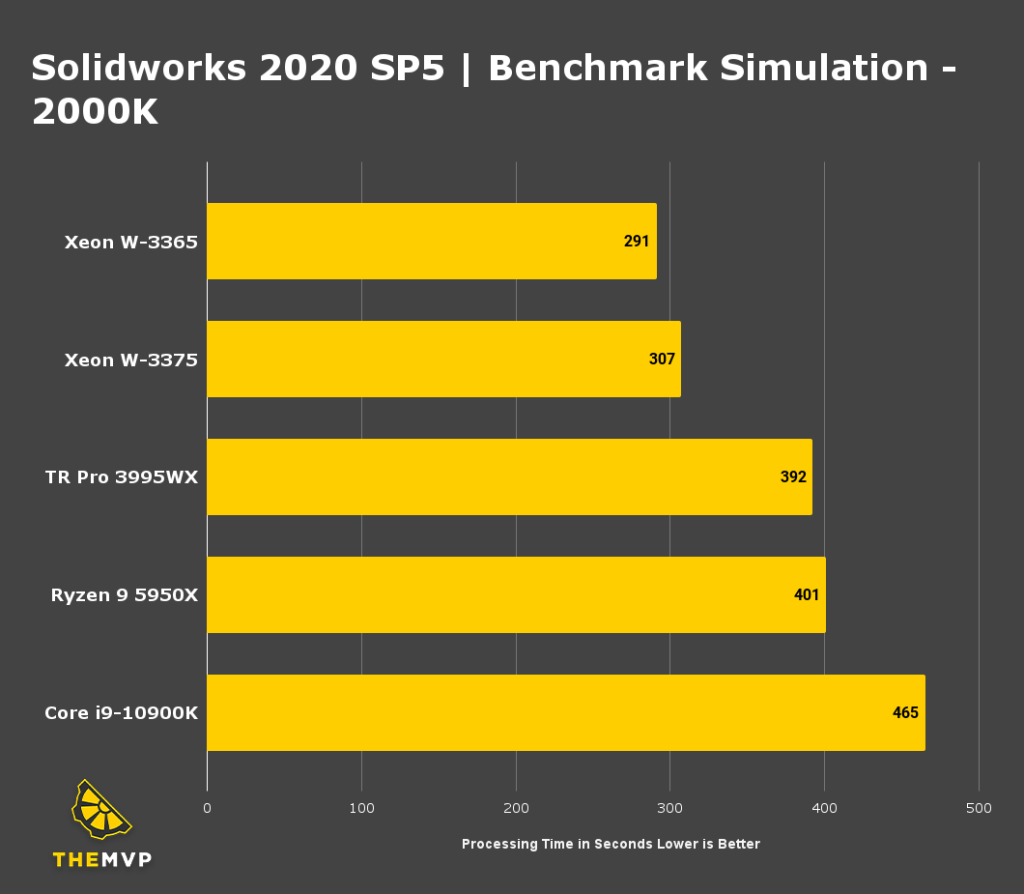
For simulation in SOLIDWORKS, the Intel Xeon W-3365 32 Core is a top choice. Simulation workloads are sensitive to both clock speed and the number of CPU cores. They also require substantial memory bandwidth and a larger overall system RAM. For this reason, Intel’s high core count Xeon W processors are ideal for simulation, particularly for FEA and Flow simulations, while still delivering excellent performance for general SOLIDWORKS modelling tasks. The additional cores in the Xeon W-3365 32 Core also enhance rendering performance with PhotoView 360. If rendering is the primary focus, even higher core count CPUs like AMD’s Thread Ripper PRO line will deliver faster results.
Will having more CPU cores enhance SOLIDWORKS performance?
When it comes to modelling and working with assemblies in SOLIDWORKS, the number of cores is not a major factor in determining performance. Our testing has revealed that the operating frequency of the processor plays a more significant role in overall performance for general modelling tasks. On the other hand, simulation and rendering can experience moderate to significant performance gains with an increased number of cores, which is why we utilise Intel Xeon W CPUs with up to 32 cores for our simulation workstations.
Is it necessary to have a Xeon CPU for SOLIDWORKS?
Some Intel Xeon processors offer higher core counts and larger memory capacities compared to the Core models, as well as support for additional instruction sets, which can enhance performance in rendering and certain types of simulation. However, Xeon CPUs generally have a lower operating frequency than Core i7 and i9 CPUs, meaning that some performance may be sacrificed for general modelling tasks. We offer workstations based on both platforms to accommodate the different needs and budget considerations of SOLIDWORKS users.
Is overclocking a suitable option for SOLIDWORKS?
As a general rule, we do not recommend overclocking for professional workstations. The modest performance increases achieved through overclocking are often outweighed by the potential downsides, such as instability, shortened hardware lifespan, and the risk of producing inaccurate data.
When it comes to video cards for SOLIDWORKS, Dassault Systemes suggests using a workstation GPU. This type of card has been found to offer significant performance benefits over other options, such as a low-end Quadro that outperforms other, faster GeForce cards. Additionally, using a certified GPU is necessary to receive official support for features like Realview and Ambient Occlusion.
Before SOLIDWORKS 2019, there was little variation in performance between different Quadro video cards, except for complex assemblies on high resolution monitors. However, with the introduction of the “Enhanced Graphics Performance” mode in SOLIDWORKS 2019, the video card plays a larger role in displaying parts and assemblies, resulting in a noticeable difference in frame rates depending on the Quadro card used.
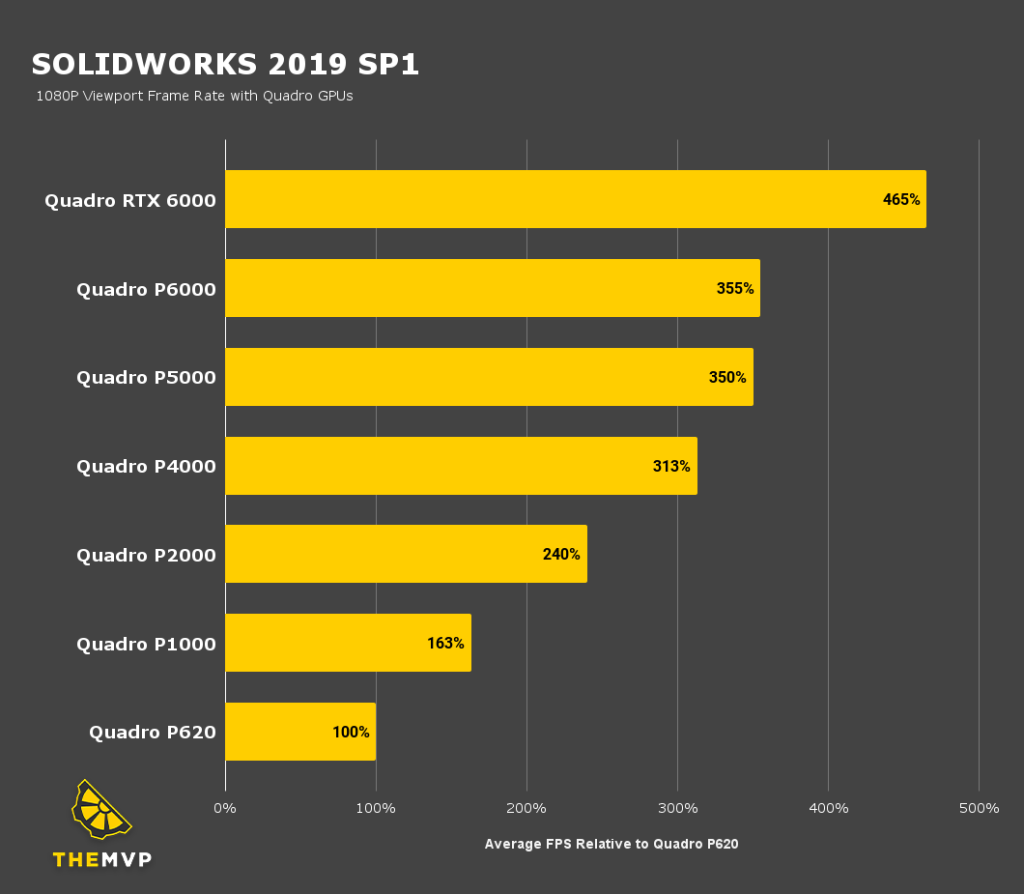
Graphics card for SolidWorks
For SOLIDWORKS, it is recommended to use a workstation card from companies like Nvidia or AMD. Our research has shown that in certain cases, a lower end Quadro card can perform better than a high-end GeForce card. To have access to features like Realview and Ambient Occlusion, it is important to use a certified card.
Before SOLIDWORKS 2019, there wasn’t a noticeable difference in performance between different Quadro video cards, except for very complex assemblies on high-resolution monitors. With the introduction of “Enhanced graphics performance” mode in SOLIDWORKS 2019, the video card plays a larger role in displaying parts and assemblies. This means that there is now a significant difference in frame rates between different Quadro cards. Based on our findings, we suggest selecting a video card that provides smooth frame rates, exceeding 30fps, for most situations, depending on model size and resolution. These are the best Graphic Card for Solidworks

Solidworks RAM Requirements
The amount of RAM needed for SOLIDWORKS can vary based on the complexity of the models being worked on. However, as a general guideline, SOLIDWORKS requires between 4-8GB of RAM for tasks such as rotating models, simulations, and rendering. To ensure optimal performance, it is recommended to have 16GB of RAM in your system.
One way to determine the necessary amount of RAM is to calculate 5GB of RAM for SOLIDWORKS and an additional 20 times the largest assembly size you work with. For example, if your assemblies are around 200MB in size, you would need a minimum of 5GB + 20 x .2 = 9GB of RAM. This formula provides the following minimum recommended RAM amounts for various assembly sizes.
Check out our catalogue of optimised Solidworks builds here.
We build and ship Custom PCs across India with upto 3 years of Doorstep Warranty & Lifetime Technical Support. We have 3 stores in Hyderabad, Gurgaon & Bangalore. Feel free to visit them or get in touch with us through a call for consultation.